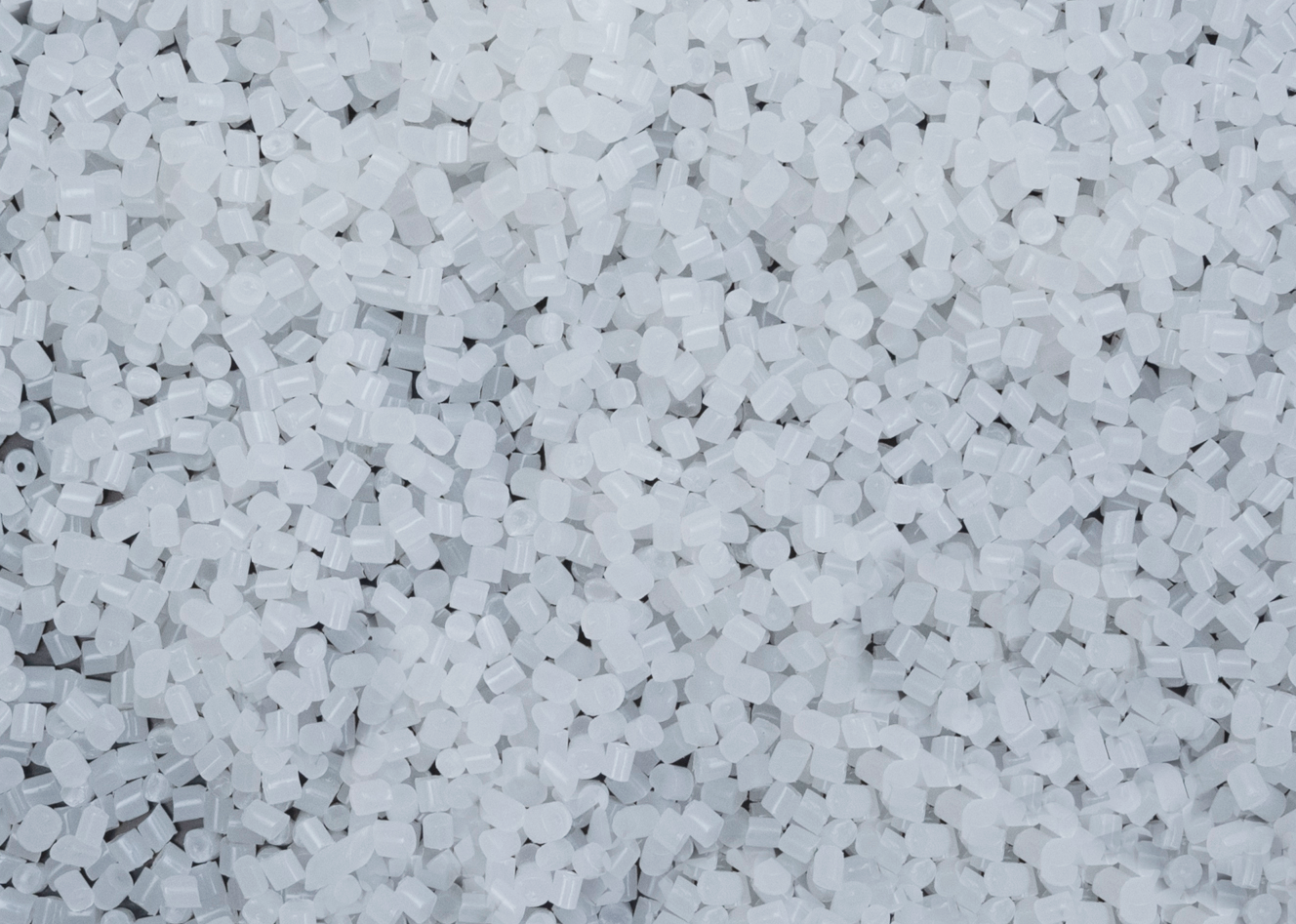
Explore Additive Masterbatch: Enhancing Products Across Industries
Table of Contents
- Introduction
- Additive Masterbatch
- Types of Additive Masterbatch
3.1 PPA Masterbatch
3.2 Slip Masterbatch
3.3 Anti-Oxidant Masterbatch
3.4 Filler Masterbatch
3.5 Anti-Moisture Masterbatch
3.6 Anti-Fog Masterbatch
3.7 Anti-Fab Masterbatch
3.8 UV Masterbatch
3.9 Optical Brightener Masterbatch
3.10 Fragrance Masterbatch
3.11 Antimicrobial Masterbatch
3.12 Odor Remover Masterbatch
3.13 Anti-Scratch Masterbatch
3.14 Anti-Shrinkage Masterbatch
3.15 Purging Compound
3.16 Silicon Masterbatch
3.17 Laser Marking Masterbatch
3.18 Flame Retardant Masterbatch - Benefits and Applications of Additive Masterbatches
- Conclusion
Introduction
Additive masterbatch plays a crucial role in enhancing various products across industries. By incorporating specific types of additive masterbatch, manufacturers can tailor their products to meet specific requirements and improve their performance, appearance, and functionality. In this article, we will explore a wide range of additive masterbatch types, understanding their definition, composition, benefits, and applications in different industries.
Additive Masterbatch
Additive masterbatch is a concentrated mixture of additives, carriers, and base resins. These masterbatches are designed to modify and enhance specific properties of plastic materials during the manufacturing process. By incorporating additive masterbatch, manufacturers can achieve desired characteristics such as improved strength, UV resistance, flame retardancy, reduced moisture absorption, and much more.
Types of Additive Masterbatch
PPA Masterbatch
- Definition: PPA (Polyphthalamide) masterbatch is a high-performance additive that improves the heat resistance and mechanical properties of plastic products.
- Composition: It consists of PPA resin and a carrier resin.
- Benefits: Enhances heat resistance, dimensional stability, and mechanical strength of plastic products.
- Applications: Used in automotive, electrical, and industrial applications that require high-temperature resistance and mechanical performance.
Slip Masterbatch
- Definition: Slip masterbatch reduces friction between surfaces, improving the slip and sliding properties of plastic products.
- Composition: It typically contains additives like fatty amides or erucamide and a carrier resin.
- Benefits: Improves surface lubrication, reduces sticking, and enhances the sliding characteristics of plastic products.
- Applications: Widely used in packaging films, bags, and other applications where reduced friction is desired.
Anti-Oxidant Masterbatch
- Definition: Anti-oxidant masterbatch prevents the degradation of plastic products caused by oxidation, enhancing their lifespan.
- Composition: It contains anti-oxidant additives and a carrier resin.
- Benefits: Delays the aging and deterioration of plastic products by protecting them from oxidative reactions.
- Applications: Used in automotive components, electrical cables, and other applications where long-term durability is crucial.
Filler Masterbatch
- Definition: Filler masterbatch is used to incorporate fillers like calcium carbonate or talc into plastic products, providing cost-efficiency and improved mechanical properties.
- Composition: It consists of filler particles dispersed in a carrier resin.
- Benefits: Increases product strength, reduces material costs, and improves dimensional stability.
- Applications: Widely employed in the production of pipes, profiles, and injection-molded parts.
Anti-Moisture Masterbatch
- Definition: Anti-moisture masterbatch is designed to reduce moisture absorption in plastic materials, preventing dimensional changes and enhancing product performance.
- Composition: It contains desiccant additives and a carrier resin.
- Benefits: Maintains product integrity by reducing the negative effects of moisture absorption, such as warping, brittleness, and degradation.
- Applications: Used in packaging films, electronic components, and products exposed to high humidity environments.
Anti-Fog Masterbatch
- Definition: Anti-fog masterbatch prevents the formation of fog or condensation on the surface of plastic products, ensuring clarity and visibility.
- Composition: It typically contains anti-fogging agents and a carrier resin.
- Benefits: Improves optical clarity by preventing fog formation, ensuring visibility in applications like packaging films, goggles, and greenhouse films.
- Applications: Widely used in the production of food packaging, automotive windows, and various transparent plastic products.
Anti-Fab Masterbatch
- Definition: Anti-fab masterbatch reduces friction and static electricity on the surface of plastic products, minimizing dust attraction and making them easier to clean.
- Composition: It contains anti-static agents and a carrier resin.
- Benefits: Reduces dust attraction, facilitates cleaning, and improves the overall appearance of plastic products.
- Applications: Used in electronic packaging, automotive interiors, and other applications where dust attraction and static electricity can cause issues.
UV Masterbatch
- Definition: UV masterbatch provides protection against ultraviolet (UV) radiation, preventing the degradation and color fading of plastic products exposed to sunlight.
- Composition: It contains UV stabilizers and a carrier resin.
- Benefits: Increases the lifespan and color retention of plastic products by shielding them from UV radiation.
- Applications: Applied in outdoor products such as garden furniture, automotive components, and building materials.
Optical Brightener Masterbatch
- Definition: Optical brightener masterbatch enhances the whiteness and brightness of plastic products, making them visually appealing.
- Composition: It consists of optical brightening agents and a carrier resin.
- Benefits: Improves the visual appearance of plastic products by enhancing their whiteness and brightness.
- Applications: Widely used in the production of films, bottles, and other plastic products that require enhanced visual aesthetics.
Fragrance Masterbatch:
- Definition: Fragrance masterbatch incorporates pleasant scents into plastic products, providing a unique olfactory experience.
- Composition: It contains fragrance oils or encapsulated fragrance microcapsules dispersed in a carrier resin.
- Benefits: Adds a delightful fragrance to plastic products, creating a sensory experience for consumers.
- Applications: Used in air fresheners, packaging, and other plastic products where scent is desired.
Antimicrobial Masterbatch
- Definition: Antimicrobial masterbatch inhibits the growth of microorganisms on plastic surfaces, reducing the risk of bacterial contamination.
- Composition: It contains antimicrobial agents and a carrier resin.
- Benefits: Helps maintain hygienic conditions by preventing the growth of bacteria, fungi, and other microbes on plastic products.
- Applications: Applied in medical devices, food packaging, and other applications where microbial contamination must be minimized.
Odor Remover Masterbatch
- Definition: Odor remover masterbatch eliminates unpleasant odors emanating from plastic products, providing a more pleasant user experience.
- Composition: It contains odor neutralizers or encapsulated odor-removing agents dispersed in a carrier resin.
- Benefits: Eliminates undesirable odors associated with plastic products, enhancing their overall appeal.
- Applications: Used in household products, automotive components, and other plastic applications where odor control is essential.
Anti-Scratch Masterbatch
- Definition: Anti-scratch masterbatch improves the scratch resistance of plastic surfaces, maintaining their appearance and durability.
- Composition: It contains additives that enhance the surface hardness and scratch resistance of plastic products, along with a carrier resin.
- Benefits: Protects plastic surfaces from scratches, ensuring long-lasting visual appeal.
- Applications: Used in electronic displays, automotive interiors, and various applications prone to scratching.
Anti-Shrinkage Masterbatch
- Definition: Anti-shrinkage masterbatch minimizes the shrinkage and warping of plastic products during the cooling process, ensuring dimensional stability.
- Composition: It contains additives that reduce the internal stress and shrinkage of plastic materials, along with a carrier resin.
- Benefits: Prevents deformation and dimensional changes, ensuring accurate product dimensions.
- Applications: Applied in injection-molded parts, extruded profiles, and other plastic products that require precise dimensions
Purging Compound
- Definition: Purging compound is used to clean and remove residues from the injection molding or extrusion machinery, improving production efficiency and reducing downtime.
- Composition: It typically contains a combination of cleaning agents, heat stabilizers, and carrier resins.
- Benefits: Cleans the machinery by removing colorants, residues, and contaminants, ensuring smoother production and minimizing material wastage.
- Applications: Used in the plastic processing industry for machine cleaning and color change operations.
Silicon Masterbatch
- Definition: Silicon masterbatch enhances the lubrication and slip properties of plastic products, reducing friction and enhancing processability.
- Composition: It contains silicone-based additives and a carrier resin.
- Benefits: Improves lubrication and slip properties, reducing friction and enhancing the flow and processability of plastic materials.
- Applications: Widely used in applications where reduced friction, improved mold release, and smooth surface finish are desired.
Laser Marking Masterbatch
- Definition: Laser marking masterbatch enables permanent marking or coding on plastic products using laser technology, offering traceability and customization options.
- Composition: It contains additives that facilitate laser marking, along with a carrier resin.
- Benefits: Enables high-precision, permanent marking on plastic products without the need for inks or labels, providing traceability and customization capabilities.
- Applications: Applied in packaging, automotive, and electronics industries for product identification, branding, and tracking purposes.
Flame Retardant Masterbatch
- Definition: Flame retardant masterbatch improves the fire resistance of plastic products, reducing the risk of ignition and flame spread.
- Composition: It contains flame retardant additives and a carrier resin.
- Benefits: Enhances the fire safety of plastic products by reducing flammability and slowing down flame spread.
- Applications: Widely used in electrical enclosures, construction materials, and other applications where fire safety is crucial.
Conclusion
Additive masterbatch is a versatile tool that empowers manufacturers to enhance their products’ properties and performance across various industries. By exploring the wide range of additive masterbatch types, their definitions, compositions, benefits, and applications, we have gained valuable insights into the role they play in improving product functionality, aesthetics, durability, and safety. As industries evolve and consumer expectations continue to rise, additive masterbatch will remain a critical component in the pursuit of innovative and high-quality plastic products.